The metal cap seal has been in service for more than 30 years
and is extensively used for sealing material containers, material
cabinets and IAEA safeguards equipment. Typically, 20 000 of these
metal cap seals are verified each year. The seal is detached in the
field and brought to IAEA Headquarters for identification. The
primary advantages are that the seals are simple, inexpensive and
easily attached or detached by an inspector. Attachment and
detachment efficiency is important to limit the radiation exposure
of the inspector. Unique identification of each seal is obtained by
visually comparing random scratches and solder smears on the inside
surface of the metal cap and by comparing the installation and
removal images.
Visual inspection of each seal is very labour intensive.
Therefore, a modernization programme for the metal seal is
currently in progress to maximize counterfeit resistance and to
detect breaches of integrity in the wire. Laser surface
authentication (LSA) provides an intrinsic material signature in a
machine readable form and the consequent ability to verify seals
with a higher degree of automation and lower error rates compared
with imagery analysis. Once all deployed seals have LSA signatures,
the full potential for on-site and/or in situ verification will be
realized. The integrity of the wire will be verified by an eddy
current probe, which is expected to be deployed for field use in
2012.
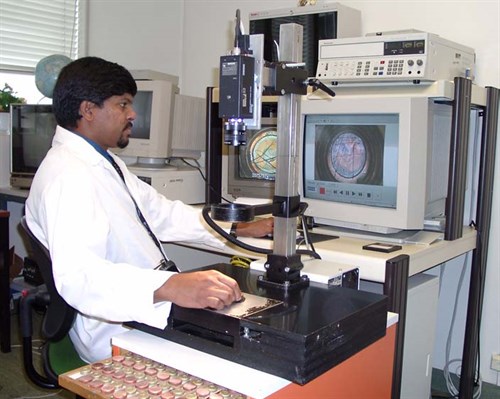
(Source: IAEA Safeguards Techniques and Equipment)
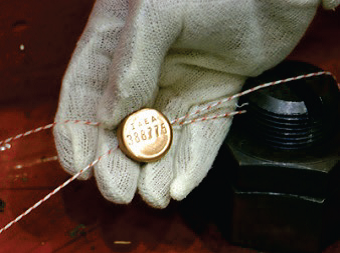
(Source: NNSA)